- January 27, 2020
- Posted by: Saddle Point
- Category: Planning and Optimization, Supply Chain Collaboration, Supply Chain Digitization, Supply Chain Visibility
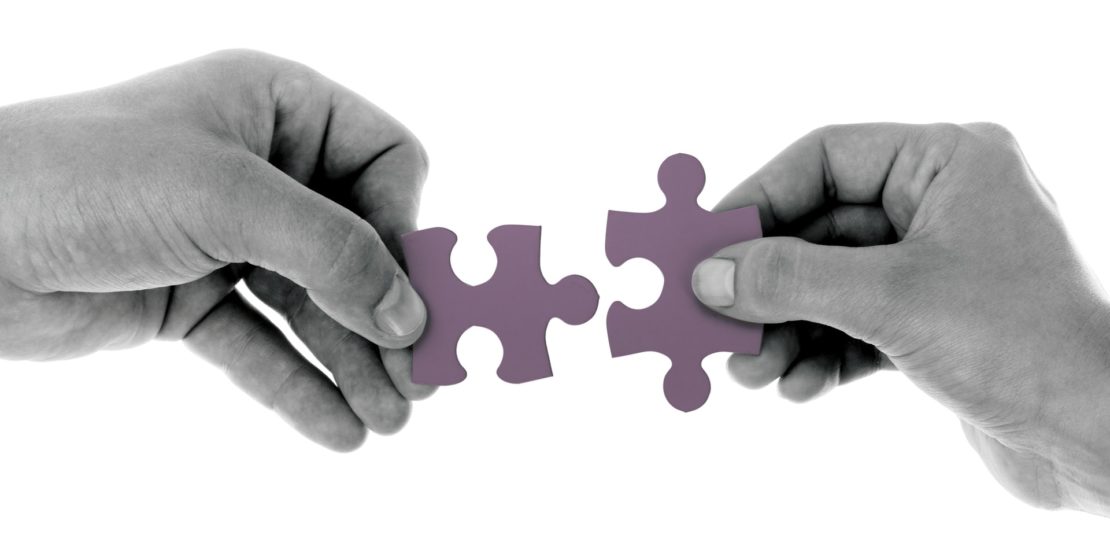
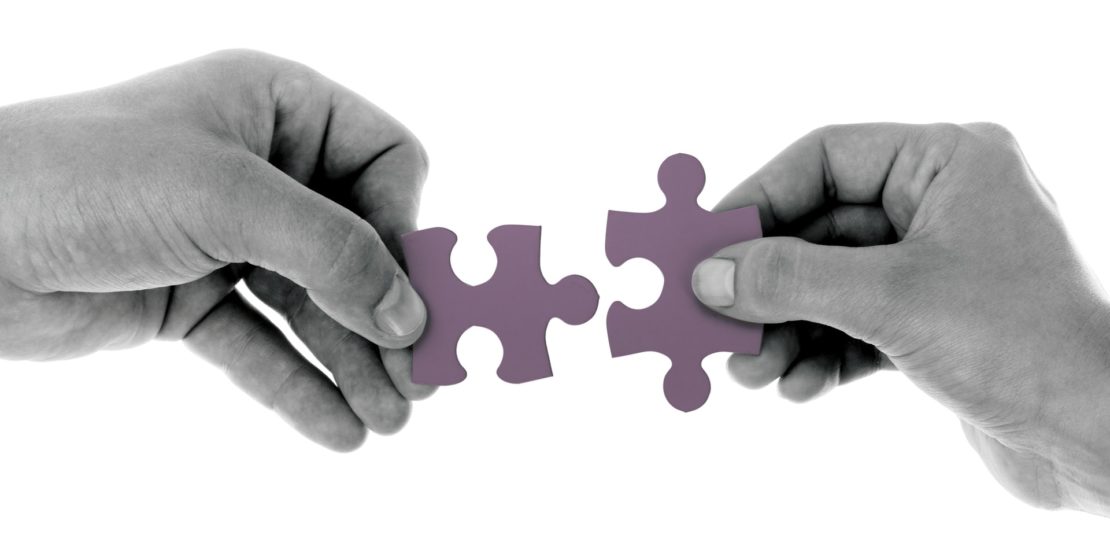
Shop floor operations are complex. Planning with variables like demand, various capacities, run rate, product mix, lead times, material constraints, etc. is not a very easy job. Throw in the element of human behavior and the complexity hits the roof. It is therefore extremely tough to do any type of root cause analysis for poor factory performance. Even though the entire shop floor is a set of interconnected operations and should behave as a shoal of fish that moves in tandem to any external stimulus, the ground reality is hardly that. Division heads, plant managers and machine operators each respond to these changes differently. » show more Theory of constraints brought in a whiff of fresh air to this complexity by laying down some very simple and easy to understand guidelines for making the shoal move in sync. The concepts of DBR and modified DBR were based on practical observations on the shop floor. TOC concepts encouraged operations managers to walk around the shop floor to visually figure out the bottle-neck resources and then subordinate all other operations to that. There were 5 steps of identifying, exploiting, subjugating, elevating and looping that formed the core of TOC. The other concept that also tries to streamline operations is mathematical modeling. By representing the physical world in terms of mathematical equations and then trying to find the best possible value mathematically gained a lot of traction in the last couple of decades. Although Mathematical modeling using Operations Research techniques was being used by the military for quite some time, it got a lot of visibility and gained a lot of traction following i2’s tremendous success. Proponents of TOC scoff at Optimization techniques as they find these to be rigid and sensitive to slight fluctuations in the inputs. The argument is that optimization techniques are theoretical and they can hardly be used in practice. There is definitely some truth in that argument. Optimization experts, on the other hand, feel that TOC is too simple as it fails to consider the varied product mix and complex production processes that have become the norm in today’s factories. With changing product mix and complex production processes, the bottleneck resources keep moving thereby throwing the basic tenet of TOC out of the window. Moreover, TOC misses out on the huge savings that can accrue if the complexities that are not humanly possible to be baked in the plan are captured mathematically and conquered programmatically. In today’s world where supply chains are getting extended with multiple stakeholders coming in, an idea of identifying bottlenecks by checking the piled up inventory before a machine might sound too simple an approach. With flexible production lines, the battle has moved to the customer which is now considered to be the only bottleneck for a business. In this changed world order, the most probable way to move forward is to capture all these variables mathematically and then make sure that certain checks and balances in terms of sensitivity analysis and scenario planning are put in place so that the flexibility of the plan is maintained. TOC can still be used in individual factories or in a smaller circle of influence. Using best of breed solutions i.e. mathematical modeling for holistic planning and then using TOC for operational level streamlining seems to be the best bet. » show less