- December 11, 2020
- Posted by: Saddle Point
- Category: Planning and Optimization
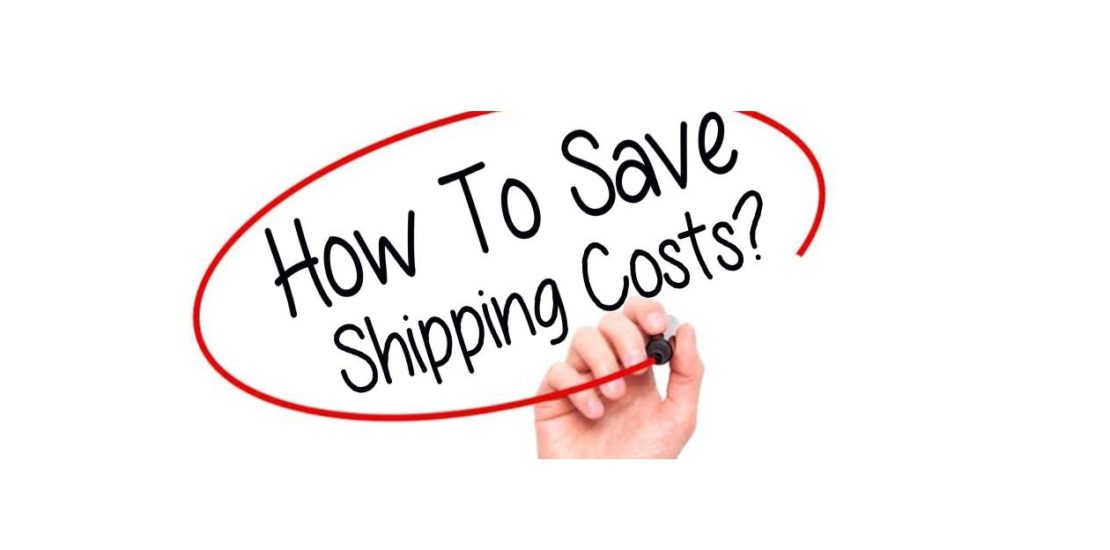
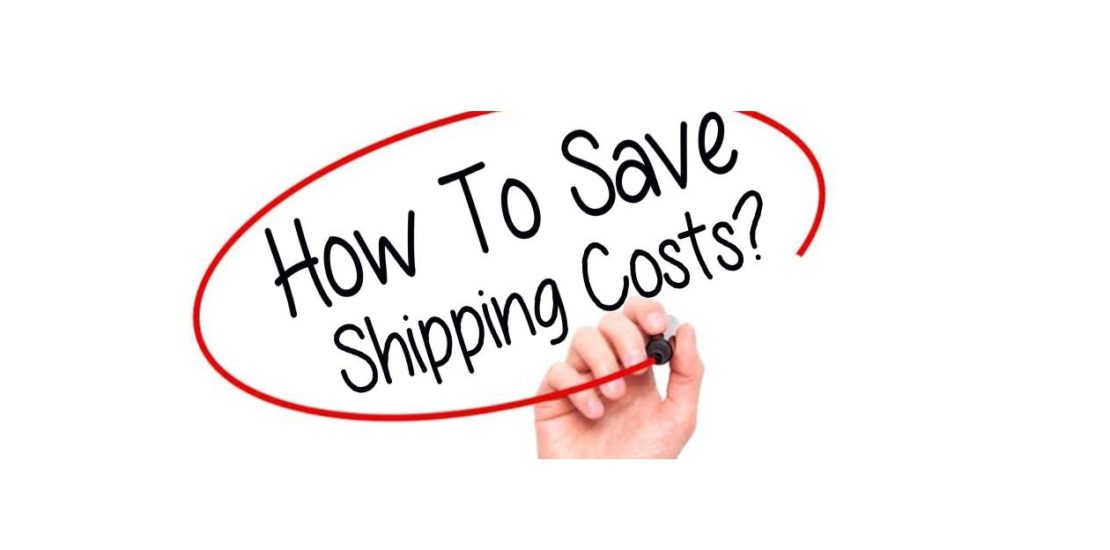
As the logistics head at Crazy Foods, Robert played a crucial role in the company’s impressive growth journey. From its humble beginnings from a 7-person startup to becoming a thriving F&B company with over 1600 employees and nationwide operations, Robert witnessed every milestone.
Robert was known for his hands-on approach to work, always ready to roll up his sleeves and dive into the operational challenges. He took immense pride in maintaining high capacity utilization of the company’s vehicles, even surpassing the required 70% capacity for each indent. By stuffing the vehicles with fast-moving SKUs, he ensured optimal performance and efficiency. However, this practice had unintended consequences.
Warehouse Challenges and the Need for Change
While Robert’s approach kept his prized key performance indicator (KPI) high, it resulted in congested warehouses and increased pressure on the warehousing team. Detention of trucks due to space constraints became a common occurrence. Realizing the need for a solution, Robert turned to his son, Jim, a senior consultant specializing in supply chain management.
Forward Looking Truck Load Building (FLTLB)
Jim’s Expert Recommendation
Jim introduced Robert to the concept of “Forward Looking Truck Load Building” (FLTLB) as a solution to the warehouse congestion problem. He explained that FLTLB involved a forward-looking approach, where the truck’s load is optimized not only for the current indent but also for the projected inventory at the destination for each SKU in the following days. By addressing potential shortages and calculating remaining space, FLTLB ensured efficient truck utilization and streamlined operations.
Cloud-Based Dispatch Optimization
Jim emphasized the importance of using a suitable tool to implement FLTLB effectively. He advised against relying solely on spreadsheets and introduced Robert to an economical yet feature-rich cloud solution that offered dispatch optimization capabilities along with FLTLB.
Streamlining Operations and Reducing Costs
Results after Implementation
Three months after implementing FLTLB and adopting the cloud-based solution, Robert and his team experienced a significant transformation in their operations. They observed a remarkable decluttering of the warehouses, as only SKUs required either immediately or in the near future were dispatched. The number of expedited shipment requests decreased considerably, providing relief during the busiest periods.
Cost Savings and Financial Benefits
The positive impact extended beyond operational improvements. The finance team reported that the total logistics costs for the past two months were 8% lower than the budgeted amount. This achievement showcased the financial benefits of optimized logistics operations.
Robert’s Legacy of Optimization
Robert’s Retirement and Sense of Fulfillment
With retirement approaching, Robert was elated to see his efforts culminate in such significant improvements. He felt a sense of fulfillment, knowing that the operations he had tirelessly built were in excellent shape and entrusted to capable hands.
Embracing Optimization for Long-Term Success
The success story of Crazy Foods highlighted the importance of adopting forward-looking strategies, such as FLTLB, to optimize logistics operations. By leveraging technology and making data-driven decisions, companies can achieve streamlined processes, reduced costs, and improved customer satisfaction.
Takeaway
The power of FLTLB lies in its ability to efficiently allocate truck space, ensure accurate inventory planning, and ultimately optimize logistics operations. Implementing this approach can help businesses overcome warehouse congestion, reduce costs, and achieve long-term success in a competitive market.