- July 7, 2020
- Posted by: Saddle Point
- Category: Planning and Optimization, Supply Chain Analytics, Supply Chain Digitization
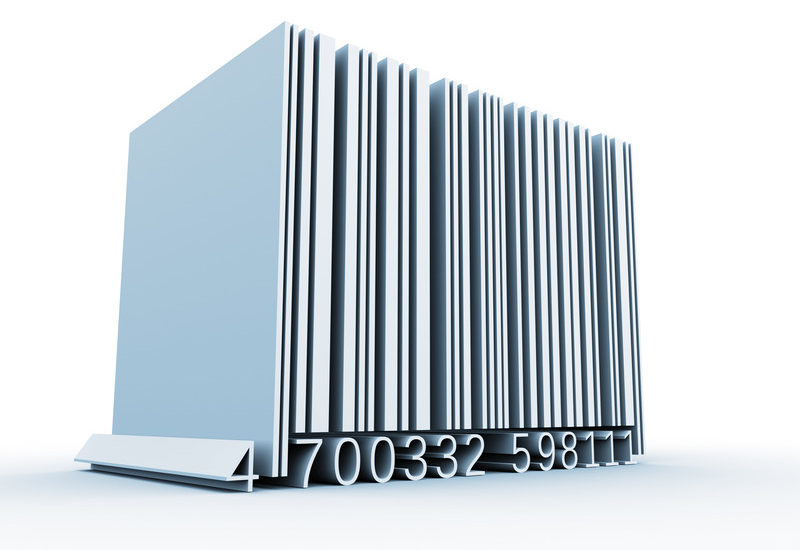
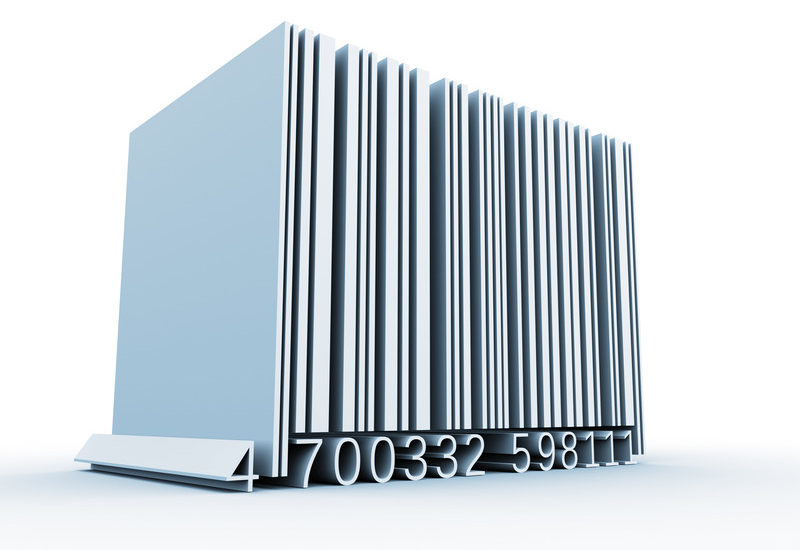
Athena, the amazing, loved mathematics. She was good with numbers. That’s why her friends fondly called her ‘The Amazing Athena’.
Athena had recently joined a large FMCG company to head the finance function. She was very happy to have got this opportunity. The company had a big product portfolio, had a bunch of star products and enjoyed very good brand equity in the market.
However, within a few weeks she was in for a rude shock. The company was a virtual sucker of working capital. With every product launch, her calls to the bankers increased. With so many good brands under it, the company had become complacent with managing inventory. On an average it was sitting on 45 days to 60 days of CFA inventory which locked up huge amount of working capital. With so much of capital locked up in inventory, she could still hear stories of late night firefighting for express shipments and cross shipments of goods from her good friend and colleague Arthur. Arthur headed the logistics function and she and Arthur bonded over Scuba diving. They regularly exchanged notes on the best locations and the best season for pursuing their passion.
Athena knew that her problems of mounting working capital costs and inventory write-off costs are invariably linked to the express shipments and cross shipments that Arthur was dealing with. In a spillover of one of their note sharing sessions, Athena and Arthur hunkered down to dissect the numbers to see where the issue was.
The company had a planning team that ran basic mathematical models in spreadsheets for calculating the demand variation and supply lead time variation over the historical horizon. These variations were then used to calculate the inventory levels. Since, it was a time consuming and resource intensive process, these numbers were therefore calculated at the beginning of every financial year and were maintained at the same level for the entire year.
Arthur explained that the variability calculated this way is not correct and it should be based on the variation that they see from the forecasted numbers. He also explained that since the variability are different for different Product~CFA and Product~MWH combination, it should be calculated at that granular level. Moreover, because of the inherent variability in demand because of product cannibalization or launch of similar products from the competitor’s portfolio etc, freezing the numbers for the entire year was not logical. Deep down he also knew that doing all these improvements in spreadsheet based planning was not practically feasible.
Arthur and Athena decided to engage a supply chain planning and optimization company to do a detailed study on rationalization of inventory and the potential reduction in working capital. The optimization company helped them determine their planned vs actual SLA, ran multiple scenarios with different data sets, generated the optimal inventory levels at the end location and then used Multi Echelon Simulation to generate the optimal inventory level at various nodes of the network.
After opting for an SLA of 99% also, they were pleasantly surprised to notice a drop of total inventory by 26%. It dropped more for some product location combinations and for some the drop was less. 26% inventory reduction, was however a significant number and had the potential to end their working capital woes overnight. When they compared the demand patterns over the year, they also realized that the inventory numbers are very much in line with the recent demand numbers as inherently the algorithms were set to give more weightage to the latest data. This was a very important observation as the old logic used one year old data to calculate inventory targets for products that were showing drastically different consumption patterns in the recent months. Arthur felt that in the VUCA world, one year old data is practically stale.
Armed with the new numbers, Arthur started pushing for the new safety stock levels in a phased manner. With service levels staying at 99%, the inventory levels started dropping. The number of express shipments also reduced drastically as each product location carried the right inventory numbers to take care of disruptions. This success created its own positive spiral and the new targets were soon rolled out to all locations.
Arthur and Athena were duly recognized by the company and were soon planning for their scuba diving vacation with their hefty year end special bonus.